12 Resin Mistakes Beginners Need to Avoid
- Bouquet Casting Co
- Oct 26, 2023
- 4 min read
You spend countless hours pouring yourself into this newfound passion and you keep hitting roadblocks. Your resin art isn't coming out how you want it to.

Drawing from a wealth of industry knowledge, this guide aims to arm you with the insights needed to navigate these challenges, outlining 12 critical mistakes to avoid in your resin art journey.
1. Using the Wrong Resin
Different projects require specialized resins. Using the wrong type can lead to issues like poor curing, lack of durability, or an undesired finish. Always consult product descriptions and reviews to select a resin that suits your specific project’s needs. Prioritize products with the ASTM D-4236 certification, ensuring they've undergone rigorous safety testing.
There is casting resin, coating resin, and UV resin that all serve different purposes.

2. Not Mixing and Measuring Accurately
Resin and hardener must be mixed in precise ratios, unique to each product. Even slight deviations can result in an uncured or uneven finish. Use graduated mixing cups and follow the manufacturer’s instructions closely, taking the time to scrape the sides and bottom of your mixing container to ensure thorough integration of the components.
Not mixing the resin and hardener completely, you could end up with uncured spots in your product. Air bubbles and color inconsistencies are also potential consequences of inaccurate mixing.
3. Too humid or Too Cold of Workspace
Temperature and humidity play crucial roles in resin curing. Ensure your workspace is within the recommended temperature range, usually around 75°F (24°C), and maintain low humidity levels. The materials themselves should also be brought to this temperature before mixing to prevent issues like bubbles or cloudiness.
If your space is too cold, the time it takes resin to cure may be extended. This could result in significantly longer curing times or an incomplete cure.
High humidity can introduce moisture into the resin, resulting in bubbles getting trapped creating an uneven surface. A white, cloudy, or foggy appearance might form on the surface of the resin, known as amine blush. This is a reaction between the hardener and moisture in the air, leading to a waxy layer on the cured resin.
4. Not Following Safety Procedures
Epoxy resins contain chemicals that can be harmful upon contact or inhalation. Always work in a well-ventilated area, wear gloves, and wear a respirator mask, especially when sanding cured resin. Remember, safety should always be your top priority.
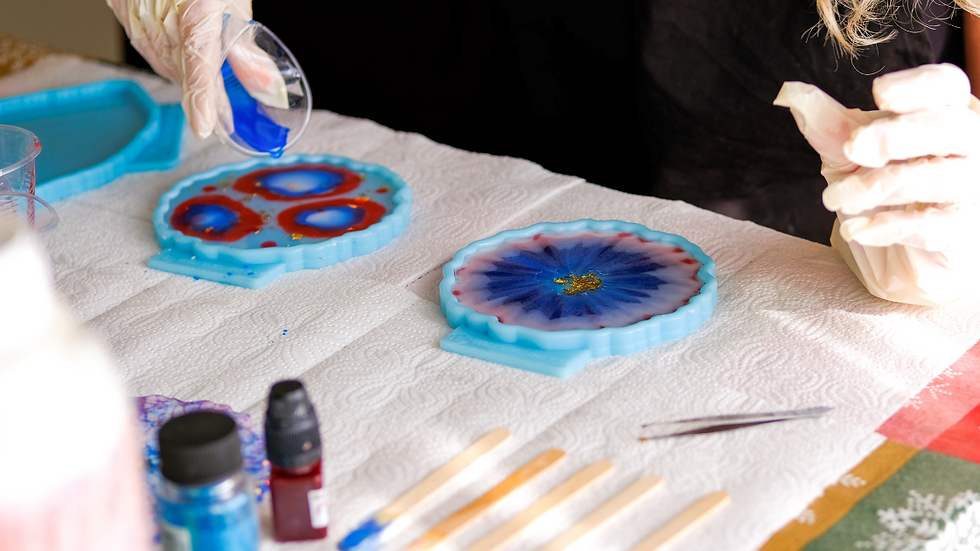
5. Adding Too Much Coloring
Resins are sensitive to moisture, and not all colorants are suitable. Make sure to use colorants designed for epoxy resin and avoid water-based products to prevent curing issues.
Experiment in small batches if you’re unsure and always follow the manufacturer’s guidelines for colorant ratios.
6. Bubbles in Your Cured Resin
Bubbles can mar the surface of your resin piece. Use a heat gun or torch to remove surface bubbles a few minutes after each pour, and pour in thin layers if working with molds to allow bubbles to escape more easily. Ensure the resin is at the correct temperature and consistency to facilitate this process.
It's impossible to get all bubbles, even the very small, out of your cured resin. The issue of eliminating as many bubbles in your resin as possible deserves it's own discussion which you can read here.

7. Misjudging Cure Times
Epoxy resins require time to cure fully. Rushing this process can lead to a sticky or incomplete cure. Familiarize yourself with the pot time and cure time of your specific resin, planning your work accordingly. The size and thickness of your pour, as well as the ambient temperature, can all impact these times. Patience is a virtue!
8. Poor Preparation
Properly prepare all surfaces before beginning your resin work. Ensure they are clean, dry, and sealed if necessary. Gather all necessary materials and tools beforehand, as the limited working time of mixed resin demands efficiency.
9. Dust and Hair Getting in Resin
Dust, pet hair, or sudden temperature changes can all negatively impact your work. Create a controlled environment, cover your work during curing, and be mindful of potential contaminants.
It's unsightly and discouraging seeing a strand of hair or specks of dust in your cured resin. Covering your resin during curing can help, but make sure to allow for a little ventilation - the resin will heat up as it cures and that heat should be able to escape.
10. Working on Uneven Surfaces
An uneven surface can lead to an uneven resin pour. Use a level to ensure your workspace and project surface are completely flat before starting your work, making adjustments as necessary.
11. Using Expired or Poor Quality Resin
Resins and hardeners have shelf lives, and their efficacy diminishes over time. Always check expiration dates and store materials in a cool, dry place. Invest in high-quality products to ensure the best results.
We recommend using Counter Culture DIY's suite of resin products.
12. Being Overly Critical
Resin art rarely turns out perfect, especially in the early stages of learning the craft. Embrace mistakes as opportunities to learn and remember that many imperfections can be sanded out or covered in a subsequent layer of resin. Don’t be afraid to repurpose ‘failed’ projects into something new and beautiful.
Mastering epoxy resin art is a journey of patience, precision, and creativity. By being mindful of these common mistakes and adhering to best practices, you can ensure your resin projects are as stunning and flawless as possible.
Remember, every artist was once a beginner, and every mistake is a stepping stone to mastery. Happy crafting!
Comments